Primus Sterilizer, based in Omaha, Neb., has been in the international spotlight recently because it’s thanks in part to their autoclave machine that the Nebraska Medical Center’s biocontainment unit has been able to successfully treat two patients that were on the front lines of the Ebola epidemic in Africa.
At the Great Bend manufacturing facility where the autoclaves are built, three buildings house a fabricating shop, welding shop, and an assembly production shop. Skilled welders, metal fabricators, machinists, and final assembly technicians with years of plumbing and electrical experience labor to create the units that are in demand by a variety of industries. Hospitals, dentist offices, pharmaceutical, FDA and veterinary facilities use the units that come in a variety of sizes.
According to a story by Steve Jordon and Bob Glissman that appeared recently in the Omaha World Herald, the decision to install a pass-through autoclave at the Nebraska Medical Center turned out to be very handy.
Treatment of Ebola waste
During the treatment of the Ebola patients, contaminated protective gear, bedsheets and the patient’s clothing was loaded in one side, sterilized and pulled out the other side to be hauled away to be incinerated. Manager Bill Tetro explained the seal between the dirty and clean side also ensures no contamination between sides.
According to Connie Mansfield, the marketing and communications manager of Primus in Omaha, the units were used continuously for 14 hours or more at a time. Staffs of 20 to 30 doctors and nurses were involved in each individual patient’s care.
“The gear, clothing, and other items that needed to be sterilized during the treatments of Dr. Rick Sacra weighed 1,011 pounds after treatment, and for Ashoka Mukpo, the free-lance cameraman for NBC, the waste weighed 1,806 pounds.
By using the autoclave, handling of the Ebola-related waste was made much simpler and effective. Since the successful treatment of these patients, Primus has seen increased interest in the company’s autoclaves by international clients. She has recently worked on a couple large projects for Africa, ground zero for the Ebola epidemic. In South America, Chili is being very forward thinking about preparing for a potential problem and she has received inquiries from there also.
Testing top priority
Thursday, workers were finishing up production of one large twin unit that will go to an unnamed location, as well as a smaller unit to go to the University of Washington for research purposes.
Brad Scheidman, a final assembly technician from Great Bend crawled under a unit ensuring the plumbing that would need to withstand steam that reached pressures as high as 450 PSI would stand up to in-plant testing.
Yards away, Rob Liles, supervisor of final assembly and shipping, also from Great Bend, prepared to do a biological test on the U of W autoclave. Liles would slip what looked like a small square of white cardboard with a black, geometric design. into the unit’s mirror-finished interior, and put it through a complete, one-hour cycle.
“If it is working correctly, the square will come out completely black,” he explained. “If it has any white spots on it, that means there is a leak somewhere, and I’ll need to go back in and find where.”
The company must meet commercial medical standards, and each unit undergoes extensive testing before it goes out the door. That’s especially important because designer Randy Doyle customizes many of the units to meet the specifications of the different customers. Primus is a small player in the industry, but has the distinction of being the only sterilizer company that wholly assembles its product in the United States, he said.
SAFETY MEASURES
Primus units used to keep Ebola contained
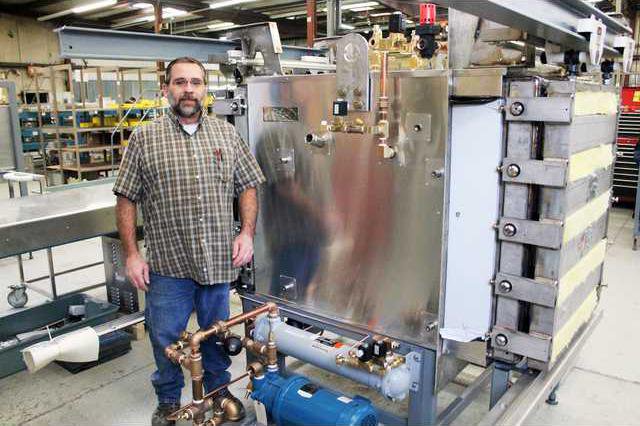
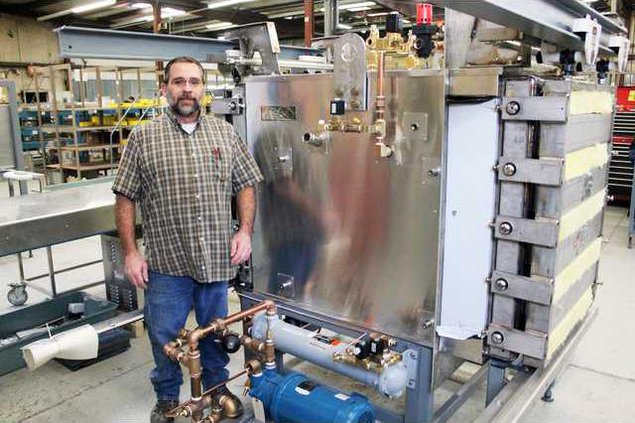